The future of refrigerants
Are you ready for the future of refrigerants?
The F-gas regulation is continuously progressing with two new bans having come into effect from 1st January 2022 but most of the implications of the legislation are still hidden by the apparent abundant supply of higher GWP refrigerants.
The purpose of the F-Gas regulation is to drive the industry to use lower GWP refrigerants, but as many of the low GWP options require different safety requirements, successful implementation will require changes in the way we work. Are you prepared for this?
A reminder of the new bans from 2022
The bans both concern systems used for ‘commercial use’ which in the regulation is defined as being “used for the storage, display or dispensing of products, for sale to end users, in retail and food services”, essentially shops and restaurants. For these applications new equipment placed on the market after 1st January which are either hermetically sealed refrigerators or freezers, or multi-compressor centralised systems with a rated capacity of 40kW or more, must use a refrigerant with a GWP of less than 150. For all other refrigeration applications, including non-hermetic retail (<40kW) and food service, the less than 2500 GWP requirement still applies.
In these times where clarity of rules and regulations is a much sought-after commodity, it would seem there is clarity within the refrigeration industry, but all is not what it seems.
The application and GWP limit bans tend to hog the limelight but lurking in the shadows is the spectre of the CO2 tonnes equivalent phasedown. Ultimately the phasedown will have the biggest impact as it will limit the quantities of higher GWP refrigerants irrelevant of the absence of any specific bans.
The challenge that the industry must deal with is determining when the next quota crunch will occur and what refrigerants will be available to use.
The second part of that question is the easier part to answer but it also potentially leads to more challenges, and not ones that can be dealt with overnight.
So what refrigerants are likely to be sustainable deep into the F-Gas phasedown and beyond to the Kigali phasedown?
The lower GWP Refrigerant choices
It has been estimated that to achieve the current F-Gas phasedown, the average GWP of refrigerants used needs to be approximately 400, and to achieve the Kigali phasedown that average drops to approximately 300. Table 1 shows a list of commercially available refrigerants with GWPs less than 700. These are likely to be sustainable under the F-Gas and Kigali phasedowns provided the refrigerants with GWPs significantly above the average are not used in large volume applications.
Table 1. – Lower GWP Refrigerants (*IPCC 100-year ITH AR4 values)
With the exception of the low-pressure refrigerants and carbon dioxide, all the refrigerants with a GWP less than 250 have a degree of flammability which, under current standards and regulations, may require additional safety measures for use. These measures may be as simple as ensuring the refrigerant change size falls within acceptable limits (BS EN 378-1:2016+A1:2020) or may require higher brazing qualifications and involvement of notified bodies (Pressure Equipment Safety Regulations 2016).
As the F-Gas regulation drives the industry to lower and lower GWP refrigerants, for those not already familiar with the requirements when using flammable refrigerants, there is no escaping the need to upskill and learn about all the requirements to safely handle and use them.
Even if it is decided to stay with non-flammable and use R-744, the brazing and notified body requirements are still a factor due to the very high pressure experienced in R-744 systems.
Standards and regulations
These have been in place for several years and equally apply to the essentially non-toxic, non-flammable (A1) higher GWP refrigerants as well as the low GWP flammable, toxic and high-pressure explosive refrigerants being considered today. The main difference is that with the previous A1 refrigerants, the safety boundaries were often well beyond the conditions of use. With the A2L, A3 and B2L safety class refrigerants these boundaries are now much closer and sometimes overlap requiring additional safety measures to be taken to ensure safe use.
Guidance on refrigerant charge size can be found in several application specific standards or, for general refrigeration or human comfort applications, BS EN 378:2016, with aids such as the Climalife A2L charge calculator online tool (www.a2l.climalife.com) available to interpret and apply the guidance. Maximum charge sizes vary dependent on refrigerant, access category, system location category and whether additional protective measures are employed or not. Although less than the higher GWP A1 refrigerants, charge sizes with A2L refrigerants can be as high as 84kg with additional protective measures and up to 17kg without any additional protective measures.
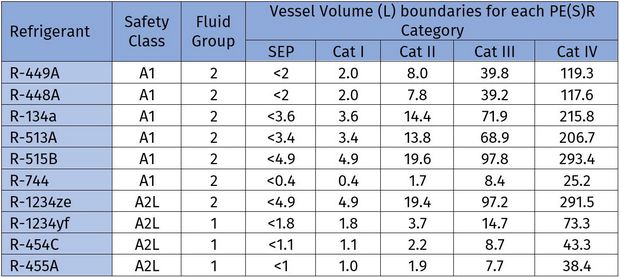
The pressure equipment safety regulation #040;PE(S)R) is also a key consideration and a legal requirement. At present PE(S)R only considers flammable and non-flammable i.e., there is no consideration of lower or higher flammability, R-1234yf is treated the same as R-290. Apart from R-1234ze, all the A2L and A3 refrigerants are in Fluid Group 1 under PE(S)R. Despite being an A2L safety class refrigerant, under PE(S)R R-1234ze is in fluid group 2 with all the A1 safety class refrigerants, as PE(S)R only considers flammability at 20°C and R‑1234ze is non-flammable at 20°C.
PE(S)R classifies pressure equipment into 5 categories depending on the refrigerant used, application/system design, pressure vessel volume, pipe size and ambient conditions. The first two categories, sound engineering practice (SEP) and Category I, only require industry standard brazing qualifications and can be self-certified, although Cat I pressure equipment does require a UKCA mark. Cat II pressure equipment requires notified body approved brazing qualification and a notified body is required to certify as well as witness a proportion of pressure tests. As the PE(S)R category increases more safety checks involving a notified body are required.
Table 2. – Examples of pressure vessel volumes and PE(S)R categories for various refrigerants in a system with an air-cooled condenser at a maximum 32°C ambient.
The management of health and safety at work and dangerous substances and explosive atmospheres (DSEAR) regulations require thorough risk assessments need to be performed. As with the previous standards and regulations already mentioned, this is not a specific requirement for flammable or high-pressure refrigerants, it applies to all refrigerants but introducing toxicity, explosive pressures or a degree of flammability may add some further elements to the risk assessment.
In summary
Whether you like it or not legislation and standards are driving the industry towards lower GWP refrigerants and no matter which route you decide to take, all the options will require a better understanding of regulations and may require further training and qualifications.
So, as you consider your refrigerant strategy for 2022 and beyond, why not commit to getting ahead of the curve and be ready for the next generation of refrigerants. Companies such as Climalife, are here to help you on that journey and can provide you with information directly and provide contacts for training institutions to upgrade your skills.