Propane heat pump hits new efficiency record
Engineers in Germany developing a propane-based refrigeration circuit for heat pumps are said to have achieved a heating capacity of 12.8kW with only 124g of propane.
A prototype of the circuit, part of the project LC150 (Low Charge 150g), is being shown by the Fraunhofer Institute for Solar Energy Systems ISE at this week’s Chillventa exhibition in Nuremberg (Hall 4A/Stand 306).
While propane has very good thermodynamic properties and low global warming potential, its flammability limits the charge size that can be safely used. According to Fraunhofer ISE, currently available heat pumps use about 60g of propane per kilowatt.
Fraunhofer ISE and a consortium of heat pump manufacturers has been building prototypes for brine heat pumps, assembling the individual components (evaporator, compressor, condenser, heat exchanger and expansion valve) in a variety of different constellations. These modules are measured on test stands 24 hours a day for two weeks at a time. Each prototype is run at between 30 and 150 operating points, and the measured values are recorded by 26 sensors. In the search for the ideal heat pump, 26 prototypes have been built so far, 14 of which have already passed through the complete measurement matrix.
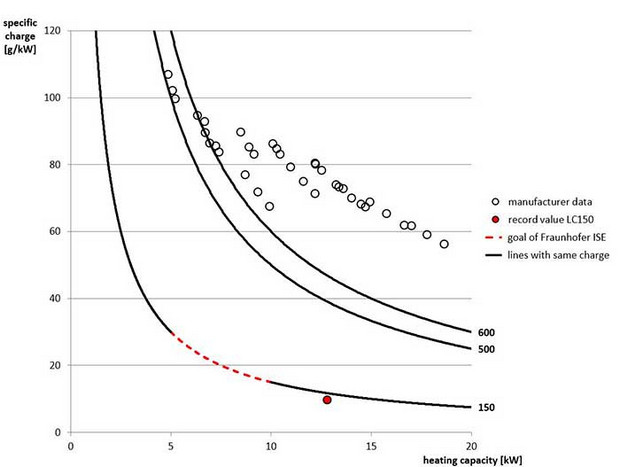
The device with the best constellation of components achieved a maximum heating capacity of 12.8kW and a COP of 4.7 with only 124 grams of propane. Achieving only 9.7g of propane per kW of heating capacity clearly exceeded the project’s goal of reducing the specific amount of refrigerant to between 15-30g/kW.
The record-breaking refrigeration circuit is not yet ready for market launch in this form, because a semi-hermetic automotive compressor was used. This requires less refrigerant at a higher capacity thanks to its high rotational speed and low oil volume. So far, automotive compressors have not been designed for the high operating hours of a heat pump that is meant to last 20 years.
The final version of the record refrigeration circuit would be implemented with slightly more refrigerant and a slightly larger heat exchanger to achieve a more balanced system, it is said. The research team insists that the goals of the LC 150 project – a refrigeration circuit with an output of 8-10kW and a maximum charge of 150g of refrigerant – can be achieved under real operating conditions.
In addition to the compressor, the research team also reduced the internal volume of the heat exchangers and the amount of oil to reduce the amount of refrigerant required. Additional components such as sensors have been kept to a minimum and the piping kept as short as possible to reduce the internal volumes.
The LC150 project is funded by the German Federal Ministry of Economics and Climate Protection (BMWK) and runs until March 2023.